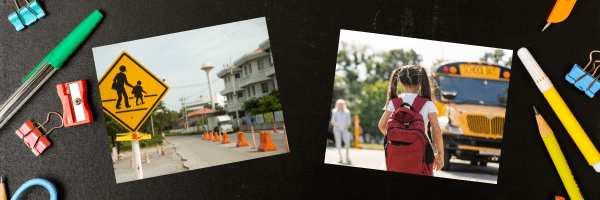
Back to School Safety Tips for Roads, Job sites & Pedestrian Zones
School’s Back – Safety Tips for Roads, Job sites & More
When the school year starts, safety becomes everyone’s responsibility—from drivers and road crews to contractors working near neighborhoods. With increased pedestrian traffic, early morning congestion, and active crosswalks, August is the perfect time to refresh your safety strategy.
Here are key safety tips and gear to help protect students, workers, and drivers.
🛑 School Zone & Pedestrian Safety
Back to school means slower speeds, higher awareness, and more foot traffic. Be prepared with:
- High-visibility vests for crossing guards, school staff, and work crews
- MUTCD-compliant road signs like “School Zone Ahead,” “Crosswalk,” and “Slow – Children at Play”
- LED stop paddles and lighted batons for increased visibility in early mornings
Tip: If you supply traffic control gear to a school district or municipality, now is the time to restock! [Link to your traffic safety gear section]
🦺 Worksite Adjustments During School Hours
If your team is working near a school, church, or residential zone, timing and visibility are critical.
- Avoid noisy equipment during school drop-off/pick-up times
- Use barricades, cones, and temporary signage to redirect traffic safely
- Make sure all workers wear Class 2 or Class 3 reflective apparel
Product spotlight: Our best-selling hi-vis cooling vest keeps your crew safe and comfortable on hot school-day mornings. [Link to product page]
🚌 Shared Responsibility on the Road
Contractors, utility crews, and drivers must all slow down and pay attention.
- Remind your team about blind spots, especially around school buses and pedestrians
- Equip trucks with backup alarms and wide-angle mirrors
- Be alert for bike traffic and younger pedestrians in crosswalks
📦 Need to Stock Up for Back to School?
Back to school safety starts here! Whether you’re a school administrator, city buyer, or contractor working near high-traffic zones, Southern Safety Supply has the gear you need:
- Traffic cones and sign kits
- Reflective apparel and accessories
- Handheld signs, paddles, and barricades
- Electrolytes and cooling gear for hot mornings
Final Tip: Partner With a Safety Supplier Who Gets It
As a small local business, Southern Safety Supply understands your unique needs. We’re here to help you protect your team—and your community—this school year and beyond.
📞 Call us at 865-673-0149 or stop by between 8:00–4:30 ET, Monday–Friday. Let’s build a safer season together.
#BackToSchoolSafety
#SchoolZoneSafety
#PedestrianSafety
#DriveAlert
#SlowDownForKids
#StayVisible
#SafetyFirstAlways
#WorksiteAwareness
#SafetyOnTheStreets
google-site-verification: googleddaf087b84679d28.html