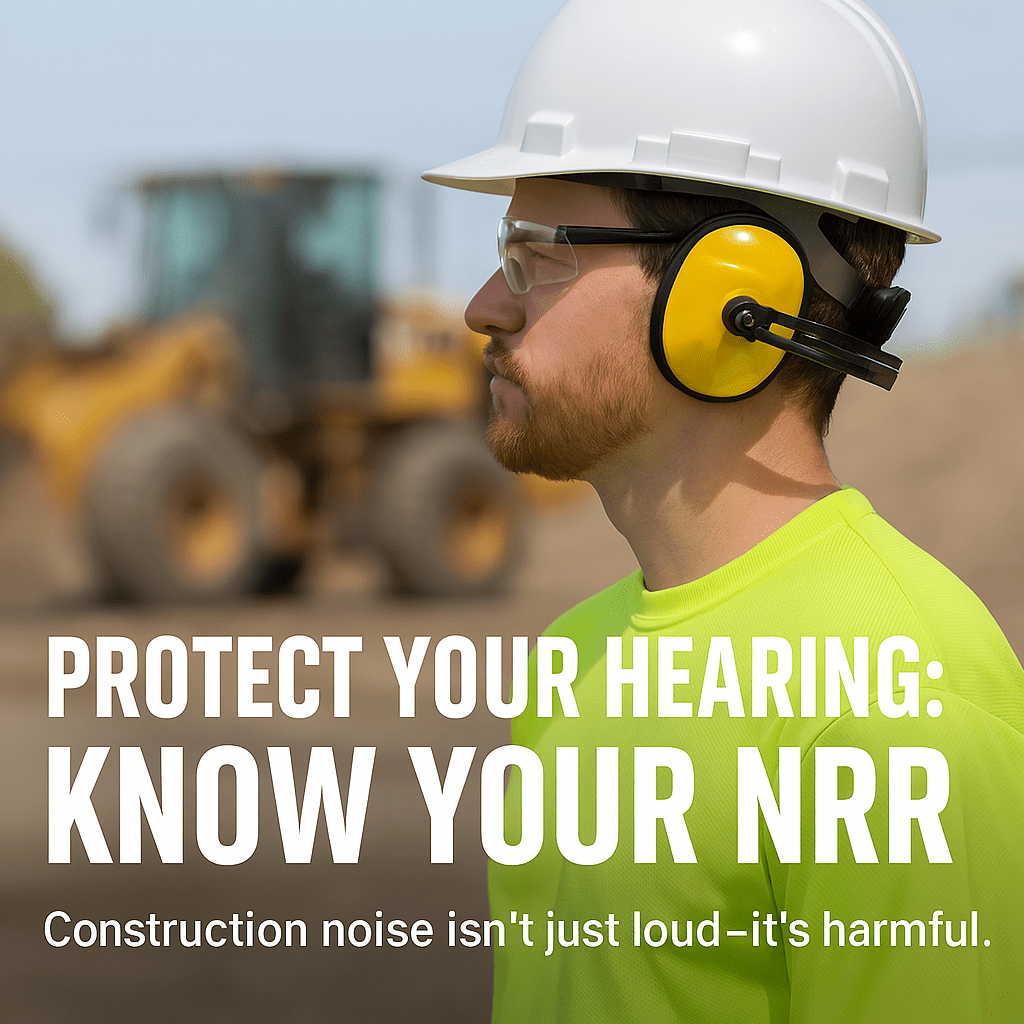
Protect Your Hearing on the Job: What Construction Workers Need to Know About Noise Reduction Rating (NRR)
If you work in construction or heavy industry, chances are you’re surrounded by high-decibel noise every day—power tools, heavy machinery, compressors, jackhammers, and more. While these are essential tools of the trade, long-term exposure to loud noise can lead to irreversible hearing damage. That’s why hearing protection for construction workers isn’t just a recommendation—it’s a necessity.
One of the most important things to understand when selecting industrial hearing protection is the Noise Reduction Rating (NRR). But what does NRR really mean, and how can you be sure you’re getting the right level of protection for your work environment?
What is Noise Reduction Rating (NRR)?
The Noise Reduction Rating (NRR) is a standardized measurement used to determine how much noise a hearing protection device (HPD) can block. It’s expressed in decibels (dB), and you’ll find it clearly marked on the packaging of earplugs and earmuffs.
For example:
- Disposable foam earplugs: NRR 29–33 dB
- Over-the-ear earmuffs: NRR 25–31 dB
- Dual protection (earplugs + earmuffs): Can achieve effective reduction beyond 30 dB
The higher the NRR, the greater the protection—in theory. However, real-world usage often doesn’t match lab-tested conditions.
Real-World Noise Reduction: What You Actually Get
On job sites, perfect use is rare. To better reflect real-world hearing protection, safety organizations like OSHA and NIOSH recommend the following calculation:
(NRR – 7) ÷ 2 = Actual dB protection
So if your earmuffs are rated NRR 30:
- 30 – 7 = 23
- 23 ÷ 2 = 11.5 dB of actual protection
This formula helps account for imperfect fit, movement, and environmental factors that reduce effectiveness.
Why Hearing Protection is Critical in Construction and Industrial Settings
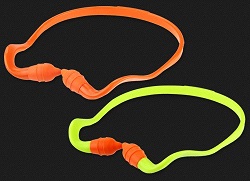
Daily exposure to sounds above 85 decibels can lead to noise-induced hearing loss (NIHL). Common noise levels on construction sites include:
- Circular saw: 100 dB
- Pneumatic drill: 110 dB
- Bulldozer: 95–105 dB
Without proper protection, even short bursts of these sounds can cause long-term damage.
Recommended Hearing Protection Products for Construction Workers
Here are a few reliable options that balance protection, comfort, and durability for industrial environments:
- 3M E-A-R Classic Earplugs (NRR 29 dB)
Great for general construction use. Comfortable, disposable, and effective. - Howard Leight Laser Lite Foam Earplugs (NRR 32 dB)
Brightly colored for visibility and compliance checks, with high attenuation. - 3M Peltor Optime 105 Over-the-Head Earmuffs (NRR 30 dB)
Heavy-duty earmuffs ideal for use around jackhammers or concrete saws. - Honeywell Sync Digital AM/FM Earmuffs (NRR 25 dB)
Combines hearing protection with built-in radio for long shifts. - 3M Peltor X5A Earmuffs (NRR 31 dB)
Designed for extremely loud environments—great for demolition or airport work.
For high-noise areas, doubling up (earplugs + earmuffs) is often required. This combo can offer significantly more protection and is standard practice in many industrial settings.
Pro Tips for Maximum Hearing Safety
- Train your team on proper earplug insertion—most underperform due to poor fit.
- Inspect and replace hearing protection regularly—foam earplugs are not meant to be reused indefinitely.
- Use signage on job sites to remind workers when and where hearing protection is mandatory.
- Monitor sound levels with a noise dosimeter if you’re unsure whether protection is adequate.
Wrap-Up: Don’t Take Chances with Your Ears
Your hearing is one of your most important tools—and it’s not replaceable. By choosing the right hearing protection for construction sites and understanding how NRR works, you can drastically reduce your risk of permanent hearing damage.
Whether you’re cutting lumber, breaking concrete, or working near heavy equipment, always wear properly rated industrial ear protection. Your future self will thank you.
Looking for more safety gear? Sign up for our email alerts or check out our full Product line for our PPE.